The gate valve is used as a cutoff medium, and when fully open, the entire flow is through, and the pressure loss during medium operation is relatively small. Gate valves are usually suitable for working conditions that do not require frequent opening and closing, and maintain the gate fully open or fully closed. Not suitable for use as a regulator or throttle. For high-speed flowing media, the gate can cause vibration of the gate under local opening conditions, which may damage the sealing surfaces of the gate and valve seat. Throttling can cause the gate to be eroded by the media.
The sealing ring connection surface is corroded and can be repaired by grinding, bonding, and other methods. If it cannot be repaired, the sealing ring should be replaced. Remove the screw pressure ring for cleaning, replace damaged components, grind the sealing and connection seat sealing surfaces, and reassemble. For components with significant corrosion damage, welding and bonding methods can be used to repair them; The sealing ring should be re welded according to the welding specifications.When repair welding is not possible at the weld overlay, the original weld overlay and processing should be removed.
A butterfly valve is a switch that rotates the valve plate 90 degrees by the valve stem, and its working principle is simple. There are various types of butterfly valves, and according to their seat forms, we can divide them into single eccentric butterfly valves, double eccentric butterfly valves, and three eccentric butterfly valves, which can be applied in different workplaces. However, how should we confirm the selection of these eccentric butterfly valves when selecting.

The plunger type globe valve is a variant of the conventional globe valve. In this valve, the disc and seat are usually designed based on the plunger principle. The valve disc is polished into a plunger and connected to the valve stem, and the sealing is achieved by two elastic sealing rings sleeved on the plunger. Two elastic sealing rings are separated by a sleeve ring and the sealing ring around the plunger is pressed firmly by the load applied by the valve cover nut on the valve cover.
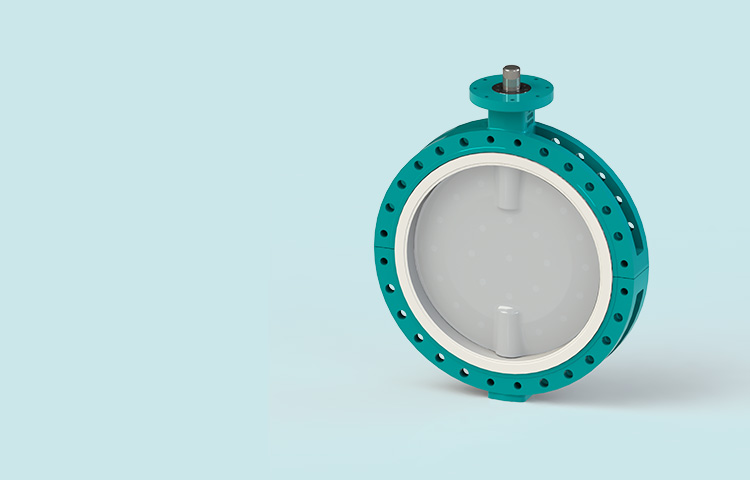
Therefore, it is necessary to add limit devices for valve opening and closing, so that during the valve opening and closing process, the bellows will always expand and contract within the design range. The harsh working environment of the bellows globe valve is also a cause of its failure. Due to the long-term operation of the corrugated pipe globe valve installed in the ship in a salt spray environment, and the frequent dripping of condensate from the upper part, the upper thrust ball bearing is corroded, and in severe cases, it can lead to contact corrosion with the valve stem.